5. Управление процессом стружкообразования
Характерные особенности процесса резания состоят:
- во-первых, в том, что лезвия режущего инструмента срезают припуск слоями, толщина поперечного сечения которых обычно меньше 1 мм (лишь на тяжелых станках толщина срезаемого слоя доходит до 2 мм и более);
- во-вторых, физико-механические свойства поверхностных слоев, которые подвергаются пластическому деформированию и превращению в стружку, отличаются от свойств исходного материала заготовки;
- в-третьих, в результате деформирования и разрушения материала срезаемого слоя происходит возникновение из монолитной массы двух новых поверхностей - одной на обрабатываемой заготовке, а другой - на срезанной стружке.
Как было рассмотрено выше, в зависимости от свойств обрабатываемого материала и условий резания различают следующие виды стружек (рис.4): сливную, суставчатую, скалывания и надлома. Однако, учитывая то, что процесс резания осложняется наличием сливной стружки, для последней используют дополнительную классификацию: ленточная прямая, запутанная; непрерывная спиральная, штопорообразная, винтовая, цилиндрическая; дробленая плоская (элементы до 3-5мм) и спиральная (элементы до 1-1,5 витков) и т.п.
Использование в современном машиностроении автоматизированных производств, станков с ЧПУ и "безлюдных" технологий сделало актуальной проблему управления процессом стружкообразования. При этом, необходимо было решить следующие основные задачи: уменьшить отрицательное влияние стружки на шероховатость обработанной поверхности и долговечность работы режущего инструмента и приспособлений; улучшить условия удаления стружки из зоны резания и транспортировки ее от станка; обеспечить безопасные условия труда рабочим.
Для решения этих вопросов российскими и зарубежными исследователями были разработаны системы автоматизированного управления (САУ) процессом стружкообразования при различных условиях резания. Конечная цель в этих работах - придать стружке (дроблением или завиванием) такую форму, которая свела бы на "нет" ее отрицательные стороны. Поскольку наибольшие проблемы возникают при сливной стружке, то на первом этапе создания САУ были предложены различные классификации форм этих стружек по степени дробления и завивания.
Стружкозавивание - процесс, который происходит из-за неравномерности деформации по сечению срезаемого слоя, причем, неравномерность еe по ширине вызывает боковые завивания, неравномерность по толщине - вертикальное завивание.
Стружкодробление - разделение стружки на отдельные элементы (различных форм и размеров), которое происходит, если в стружке возникают напряжения (s>[s ]изг) больше предельно допустимых для обрабатываемого материала. Наиболее известны следующие способы дробления (завивания) сливной стружки:
- управление геометрией режущего инструмента,
- назначение режимов резания в пределах области устойчивого стружколомания,
- использование инструментов с лунками, уступами и накладными стружколомами на передней поверхности,
- использование схем резания, позволяющих получить стружку заданных размеров,
- управление динамикой резания,
- управление кинематикой резания.
Управление геометрией режущего инструмента. Этот способ наиболее эффективен при использовании инструментов с перетачиваемой режущей частью. Известно, что наибольшее влияние на процесс стружкообразования оказывают: передний угол, главный угол в плане и угол наклона режущей кромки.
Уменьшение переднего угла γ до его отрицательных значений γ =+5...-10 дает возможность увеличить деформации срезаемого слоя и в зависимости от предела прочности обрабатываемого материала и напряжений, возникающих в стружке, создаются условия для завивания или ломания стружки. Изменение переднего угла достигается заточкой либо всей передней поверхности, либо фаски под заданным углом, либо установкой на передней поверхности накладных стружколомов (рис.17).
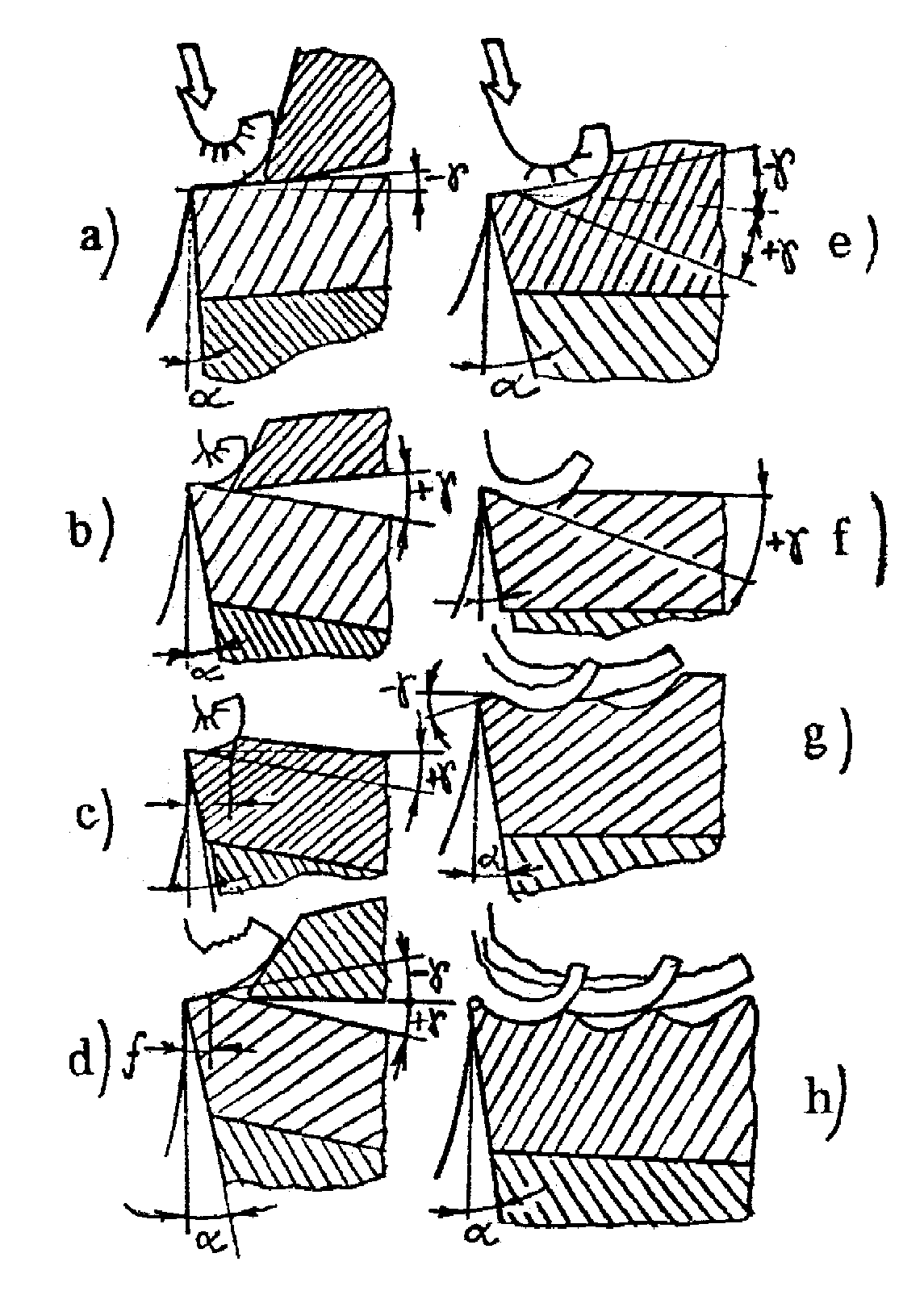
Рис.17. Формы передней поверхности инструмента:
- плоская с накладным стружколомателем и отрицательным углом γ;
- то же с положительным углом γ;
- с порожком;
- с отрицательной фаской и накладным стружколомателем;
- с лункой и отрицательным углом γ;
- с лункой и положительным углом γ;
- с двойной лункой;
- с тройной лункой
Как правило, размеры фаски "f" должны быть меньше толщины срезаемого слоя "а". Однако, необходимо учесть, что с уменьшением переднего угла возрастают силы резания и, соответственно, нагрузки на деталь и инструмент.
Увеличение главного угла в плане до значений j =90 также приводит к возрастанию деформации ε0 в структуре и способствует ее завиванию. Отрицательные факторы в этом случае - уменьшение прочности и ухудшение теплоотвода в районе вершины резца.
Изменением величины угла наклона режущей кромки l управляют не только формой стружки, но и определяют направление ее движения. Положительные углы увеличивают деформацию ε0 срезаемого слоя, что ведет к завиванию или ломанию стружки и способствуют движению стружки в направлении обрабатываемой поверхности. Отрицательные факторы: возрастание сил резания и увеличение шероховатости обработанной поверхности детали.
При отрицательных углах l стружка движется в направлении обрабатываемой поверхности, однако, вероятность получения стружки желаемой формы связана, в основном, с механическими характеристиками обрабатываемого материала. Отрицательные факторы: уменьшение прочности и ухудшение теплоотвода в районе режущей кромки.
Геометрические способы управления стружкообразованием дают возможность эффективно управлять, в основном, формой стружки.
Назначение режимов резания в пределах области устойчивого стружколомания. Этот способ наиболее эффективен при использовании инструментов со сменными (поворотными) многогранными пластинками (СМП), имеющими различные количество граней (режущих кромок) и формы передней поверхности. Учитывая высокую себестоимость инструментов на базе СМП, современные инструментальные фирмы стремятся установить для каждого типа СМП эффективные области применения, в первую очередь, с учетом возможностей устойчивого стружкодробления. Известно, что наибольшее влияние на процесс стружкообразования из режимов резания оказывают величины подачи и глубины резания. Поэтому, как правило, зоны устойчивого дробления стружки определяют путем испытания СМП различных форм в координатах: глубина резания t и величина подачи S (при постоянных: скорости резания V, геометрии инструмента, форме СМП и других факторах). В этом случае для каждого типа СМП создается специальная карта (диаграмма), по которой легко установить диапазоны режимов резания с устойчивым стружкодроблением. После проведения каждого эксперимента форма стружки фиксируется с позиций травмоопасности, возможностей транспортировки и влияния на условия работы технологической системы и классифицируется по этим признакам для каждого сочетания подача-глубина резания проведенного эксперимента. Диаграммы с зонами устойчивого стружкодробления, построенные для выпускаемых инструментальной промышленностью сменных многогранных пластин (рис.18 и 19), позволяют решить вопрос об управлении процессом стружкообразования на стадии подготовки программ для станков с ЧПУ.
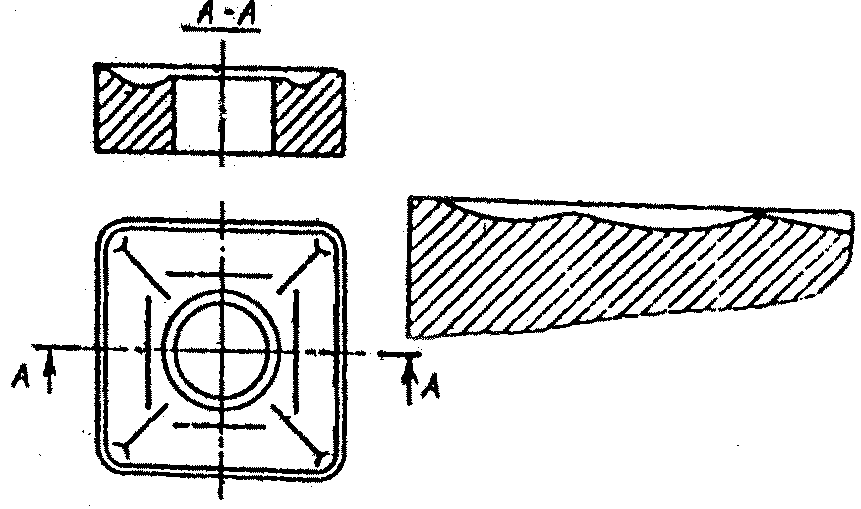
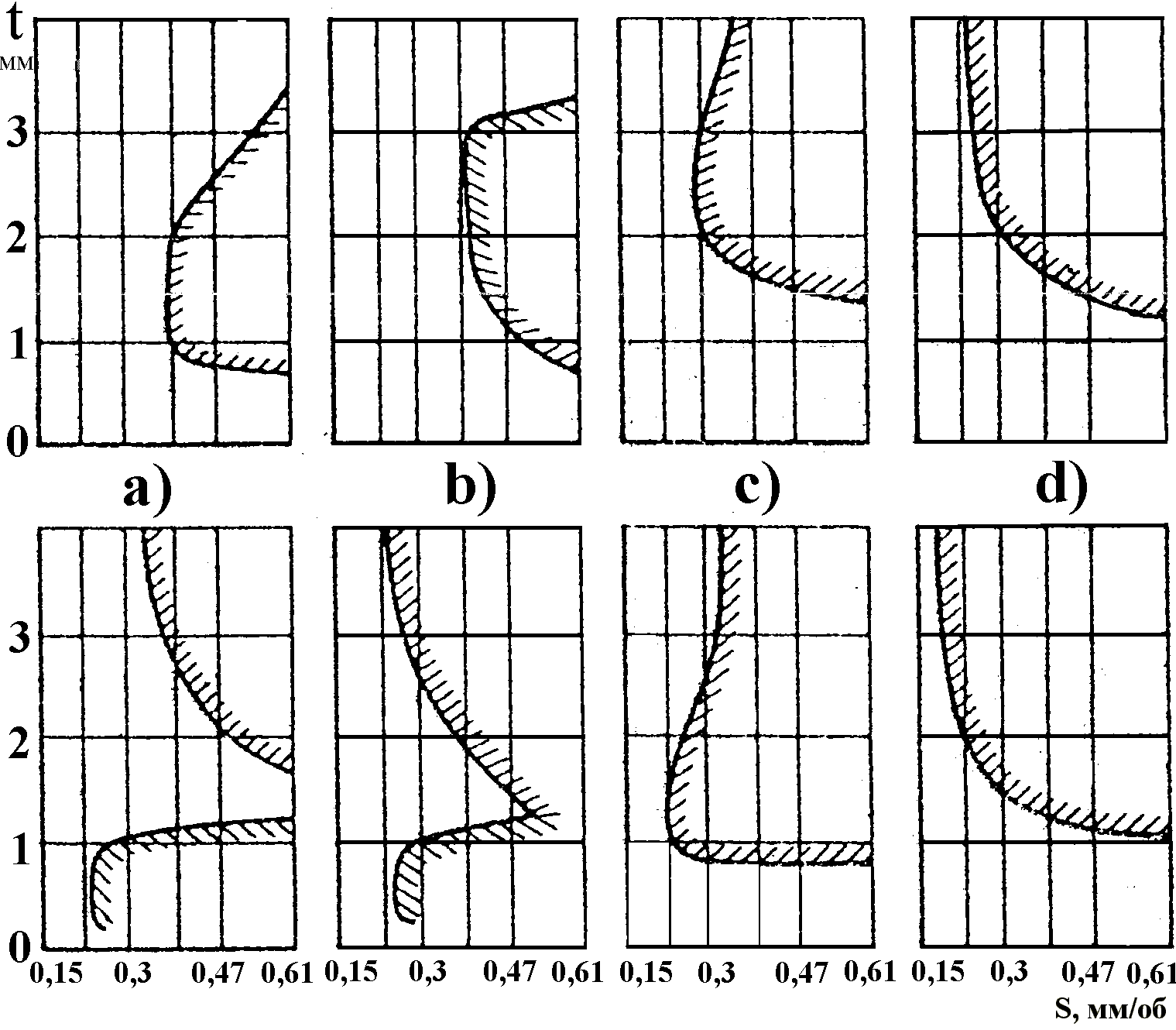
Рис.19. Диаграммы стружкодробления для резца с типовой СМП и углами в плане: φ=45 (а), φ=60 (b), φ=75 (c), φ=90 (d),
Основными достоинствами таких диаграмм являются наглядность и простота использования.
Использование инструментов с лунками, уступами и накладными стружколомами на передней поверхности. Эти изменения конструкции инструмента дают возможность устанавливать при резании удобные форму, размеры и направление движения стружки, за счет резкого увеличения деформаций по ее ширине и толщине. Лунки и уступы формируются как на инструментах, подвергаемых заточке, так и на сменных многогранных пластинках.
На затачиваемых инструментах действующими стандартами предусматриваются либо одинарные (для малых подач), либо двойные канавки (для больших подач). Количество уступов на сменных многогранных пластинках определяется их формой, размерами и назначением инструмента. Конструктивные особенности передней поверхности нестандартных СМП составляют, как правило, "ноу-хау" фирмы производителя, так как определяют условия стружкообразования при резании.
Использование схем резания, позволяющих получить стружку заданных размеров. Управление процессом стружкообразования путем выбора схем резания применяется при больших величинах толщины или ширины срезаемого слоя. В этом случае влияние на процесс стружкообразования осуществляется изготовлением стружкоразделительных канавок на режущих кромках инструмента или путем предварительного нарезания кольцевых (винтовых) канавок на обрабатываемой поверхности детали. Количество, формы и размеры стружкоразделительных канавок на режущей кромке определяются типом режущего инструмента, свойствами обрабатываемого материала и припуском на механическую обработку. Для некоторых инструментов, например протяжек, форма, размеры и количество канавок устанавливаются государственными или заводскими стандартами.
Управление динамикой резания. Изменение динамических параметров в системе инструмент-деталь-станок позволяет оказать существенное влияние на форму стружки и износ инструмента. Наиболее эффективным в этом плане, оказалось наложение на режущий инструмент в процессе его работы ультразвуковых или низкочастотных колебаний. Причем, исследования показали, что ультразвуковые колебания эффективны при работе токарных резцов и алмазных сверл, а низкочастотные- при глубоком сверлении.
Основные недостатки этого способа - необходимость установки дополнительного оборудования и его высокая себестоимость.
Управление кинематикой резания. Широкое применение в машиностроении станков с ЧПУ и инструментов со сменными многогранными пластинками (СМП) позволило использовать для управления процессом стружкообразования различные виды прерывистой (дискретной) подачи. Этот способ дает возможность получать желаемую по форме и размерам стружку независимо от режимов резания и геометрии режущего инструмента путем периодического останова или отвода инструмента от поверхности резания.
Наиболее часто используются схемы обработки со следующими видами дискретной подачи инструмента (рис.20): с кратковременным остановом- рекомендуется при обработке малопластичных материалов на черновых и получистовых операциях и с отводом под углом - рекомендуется при обработке вязких материалов. Кроме этих вариантов, находит применение дискретная подача с отводом по векторному треугольнику - рекомендуется при обработке сложно-профильных (фасонных) поверхностей; с отводом по окружности - для чистовых операций.
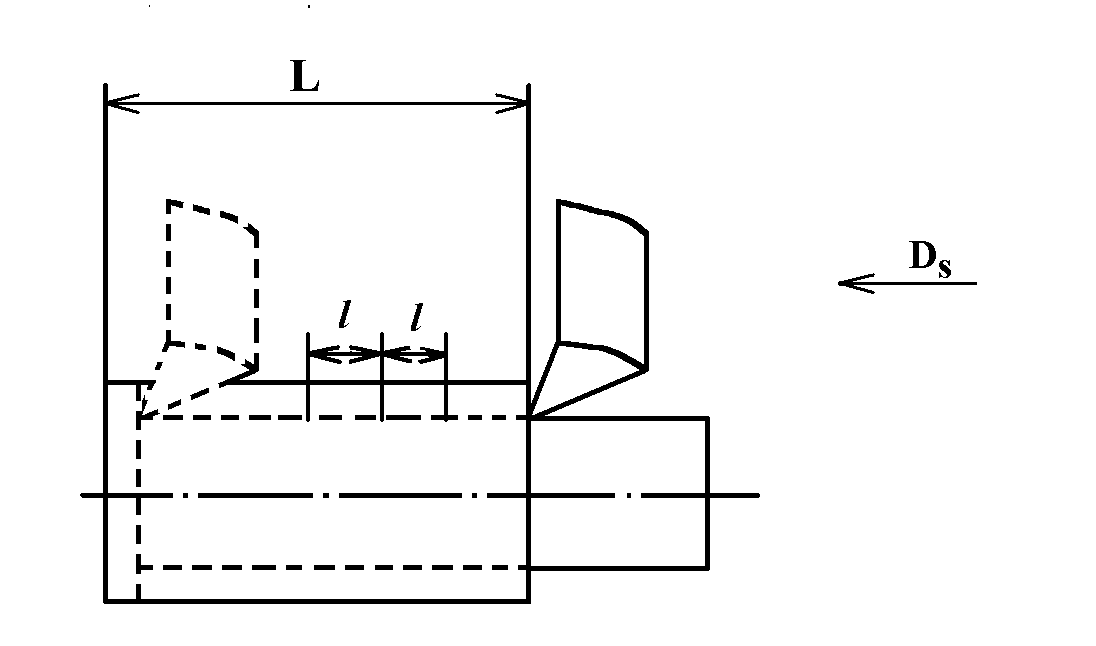
a) с кратковременным остановом
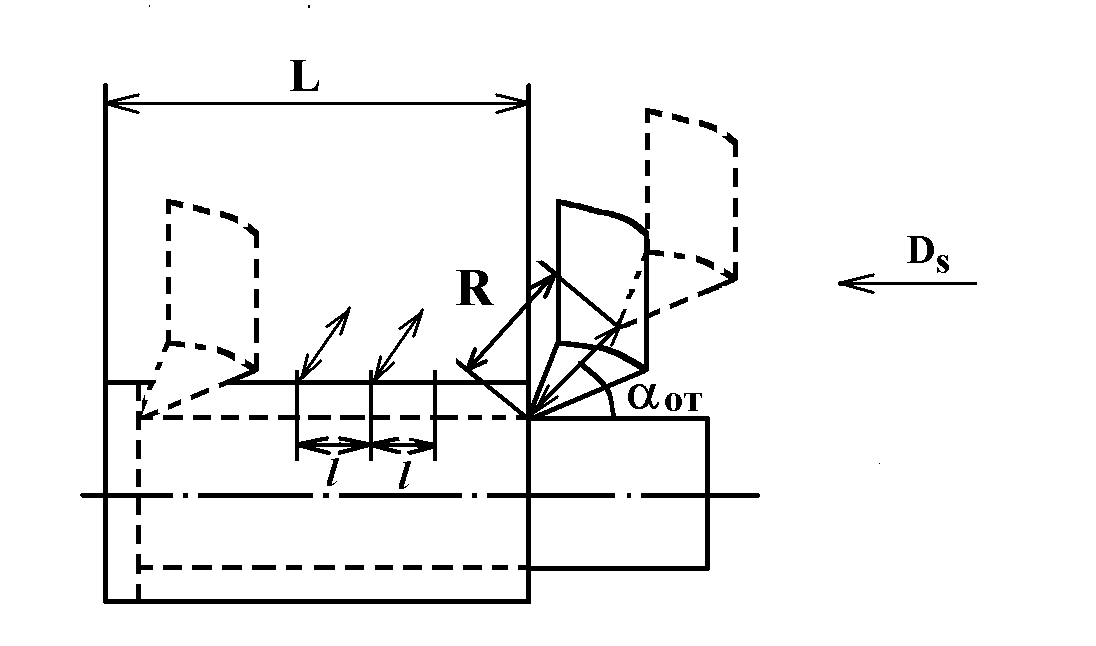
b) с отводом под углом
Рис.20. Способы кинематического дробления стружки
Дискретная подача с кратковременным периодическим остановом характеризуется тем, что через определенное расстояние l, как правило, большее величины подачи S, производится кратковременный останов инструмента в течение заданного промежутка времени t. На станках с ЧПУ программирование выбранного вида дискретной подачи осуществляется на этапе разработки управляющей программы. Основные недостатки этого способа связаны с увеличением шероховатости Rа обработанной поверхности и времени на обработку детали.