2. Физические явления, возникающие при резании
2.1. Силы резания при механической обработке
При внедрении в материал режущего инструмента на его переднюю и заднюю поверхности действуют нормальные силы N1, N2 и силы трения F1, F2 (рис.2.). Считая клин абсолютно жестким телом, можно после сложения всех сил получить общую равнодействующую силу R, являющуюся силой сопротивления резанию. Учитывая сложностиопределения нормальных сил и сил трения, для удобства расчета технологических параметров процесса резания силу R раскладывают в трехосной системе координат X-Y-Z на составляющие, которые измеряют динамометром или рассчитывают по эмпирическимформулам. При свободном ортогональном резании таких составляющих две: в направлении вектора скорости резания - Pz и перпендикулярно поверхности резания - Py.
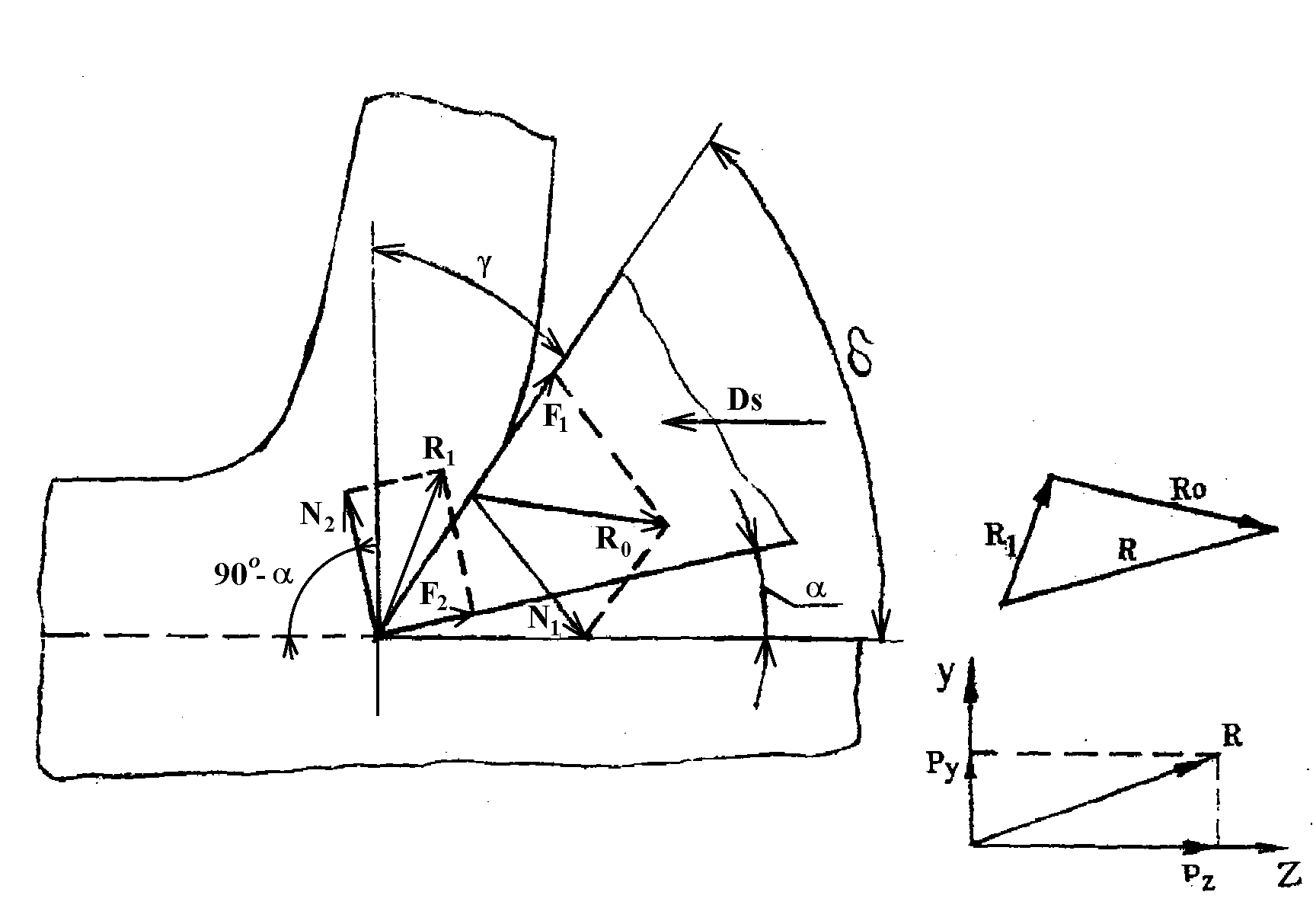
Рис.2. Схема сил, действующих на режущий клин.
Для практических целей обычно используется не сама равнодействующая сила R, а ее составляющие Рz, Рy, Рx (рис.3). При этом: величина силы Рz определяет крутящий момент резания, по которому определяются: мощность станка, параметры зубчатых колес и валов механизма скоростей станка, параметры зуба и корпуса режущего инструмента; от величины силы Рy зависят: прогиб обрабатываемой детали и ее точность, параметры деталей механизма поперечной подачи; величина силы Рx является исходной для расчета параметров деталей механизма продольной подачи станка. Кроме этого, составляющие силы резания используются при расчетах параметров шпиндельного узла и жесткости станка.
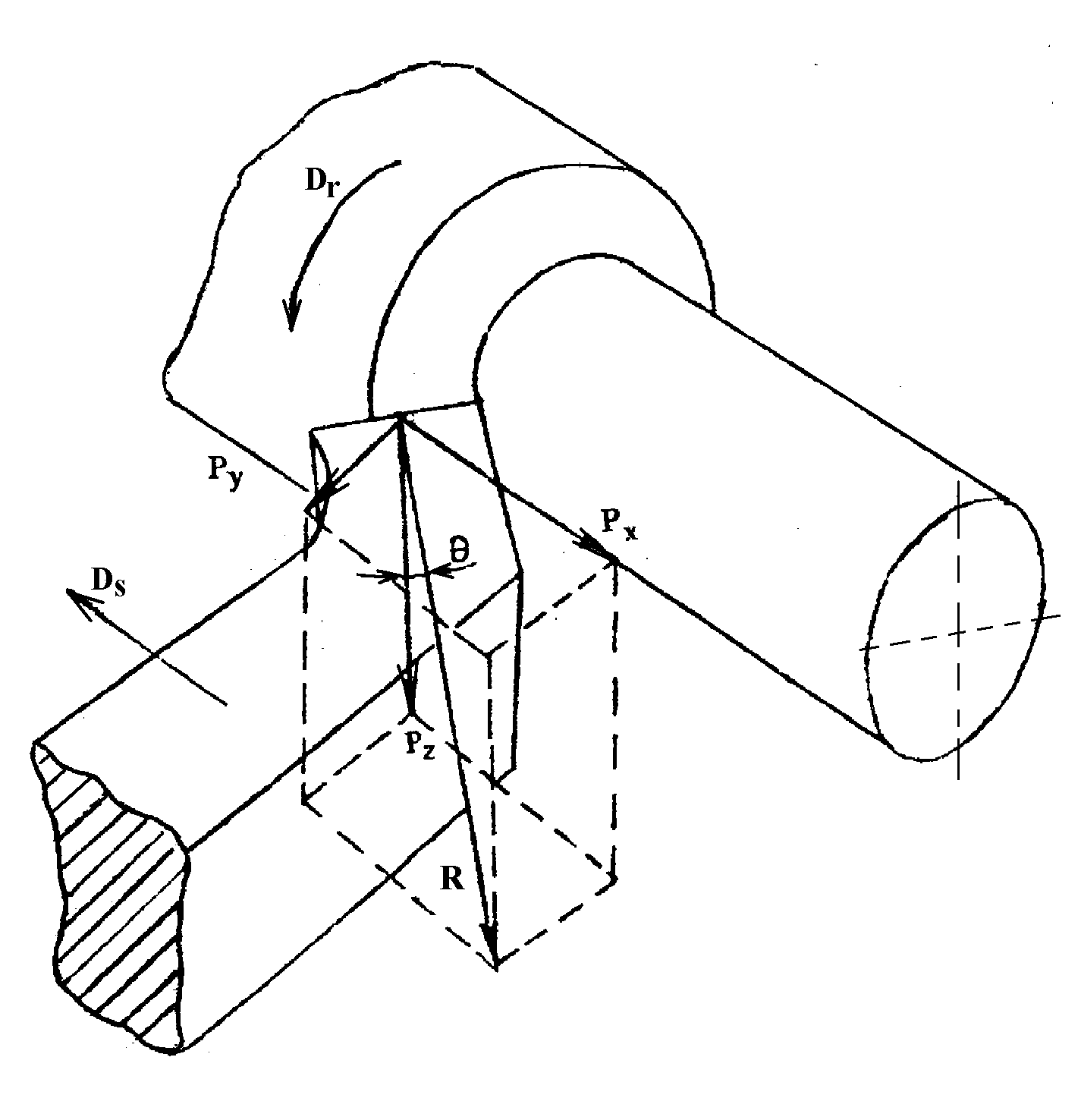
Рис.3. Разложение силы резания R на три составляющие.
Три указанные составляющие силы резания взаимно перпендикулярны; поэтому величина и направление равнодействующей силы определяются как диагональ параллелепипеда
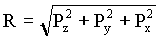
Соотношение величин составляющих сил Pz, Py, Px не остается постоянным и зависит от геометрических параметров рабочей части резца, элементов режима резания (v, t, s), износа резца, физико-механических свойств обрабатываемого материала и условий резания.
Отношения Py/Pz и Px/Pz возрастают с увеличением износа резца; увеличение подачи увеличивает отношение Px/Pz; уменьшение главного угла в плане увеличивает отношение Py/Pz. В некоторыхт случаях обработки одной из двух составляющих (Px или Py) может и не быть. Например, при разрезке прутка отрезным резцом отсутствует сила Px; при подрезке торца трубы резцом с φ=90º и λ=0º отсутствует составляющая Py. Сила Pz действует во всех случаях, и поэтому ее часто называют главной составляющей силы резания или просто силой резания.
Удельная сила резания и коэффициент резания. Для приближенного определения силы резания Pz может быть использовано уравнение
Pz = pf, Н
где f - площадь поперечного сечения среза в мм2; p - удельная сила резания (Н/мм2).
Удельная сила р численно равна силе резания, отнесенной к 1 мм2 сечения срезаемого слоя. Так как величина удельной силы зависит от элементов режима резания (v, t, s), геометрических параметров инструмента и условий обработки, значения р, полученные в различных условиях, не могут быть сопоставимы. Поэтому для расчета величин сил резания, как правило, используются различные варианты эмпирических зависимостей. Наиболее часто используется следующая типовая формула:

где i=x,y,z; Cpi, xpi, ypi, kpi - справочные коэффициенты, зависящие от свойств инструментального и обрабатываемого материалов, геометрии инструмента и т.д; t - глубина резания (мм); s - величина подачи (мм/об).
Аппаратура для измерения сил резания. Для экспериментального определения сил резания и изучения влияния на них различных факторов применяют специальные динамометры. Различают динамометры трехкомпонентные для измерения Pz, Py и Px; двухкомпонентные для измерения Pz и Py или Pz и Px и однокомпонентные для измерения какой-либо одной составляющей силы резания.
Динамометры в зависимости от принципа работы делятся на электрические, механические и гидравлические. Каждый динамометр включает в себя устройство для разложения равнодействующей силы резания на составляющие, датчики для преобразования измеряемой силы в удобно наблюдаемую величину и регистрирующее устройство. Наибольшее применение имеют электрические динамометры: пьезоэлектрические, емкостные, индукционные и динамометры с проволочными датчиками сопротивления.
2.2. Деформирование и разрушение материалов при резании
Деформации при резании распространяются впереди инструмента: в деталь и в стружку. Размеры деформированной области и характер стружкообразования зависят от свойств обрабатываемого материала и условий резания (рис.4). Если при обтекании клина материалом образуется сплошная стружка без разрывов и больших трещин, то в этом случае она называется сливной стружкой. Такой тип стружки чаще всего образуется при резании вязких, пластичных материалов. В том случае, когда при резании пластичных материалов имеет место интенсивное трещинообразование, происходит полное разделение стружки на элементы, имеющие определенную правильную форму и последовательность образования, такой тип стружки называется элементной стружкой, или стружкой скалывания.
Очень часто при резании пластичных материалов образуются стружки, не имеющие четко выраженных признаков сливных или стружек скалывания. При их образовании не происходит полного разделения на элементы и трещины заканчивают свое развитие в толще деформированного материала, не выходя на его наружную поверхность. Такие стружки называют суставчатыми.
При резании хрупких материалов (чугуна, бронзы, керамических материалов и др.) происходит вырывание отдельных частиц поверхностного слоя заготовки режущей частью инструмента. Так как пластического деформирования практически не происходит, то элементы стружки, образующиеся в процессе хрупкого разрушения, не имеют правильной формы. Обработанная поверхность шероховатая с зазубринами и вырывами. Такой тип стружек носит название стружек надлома.
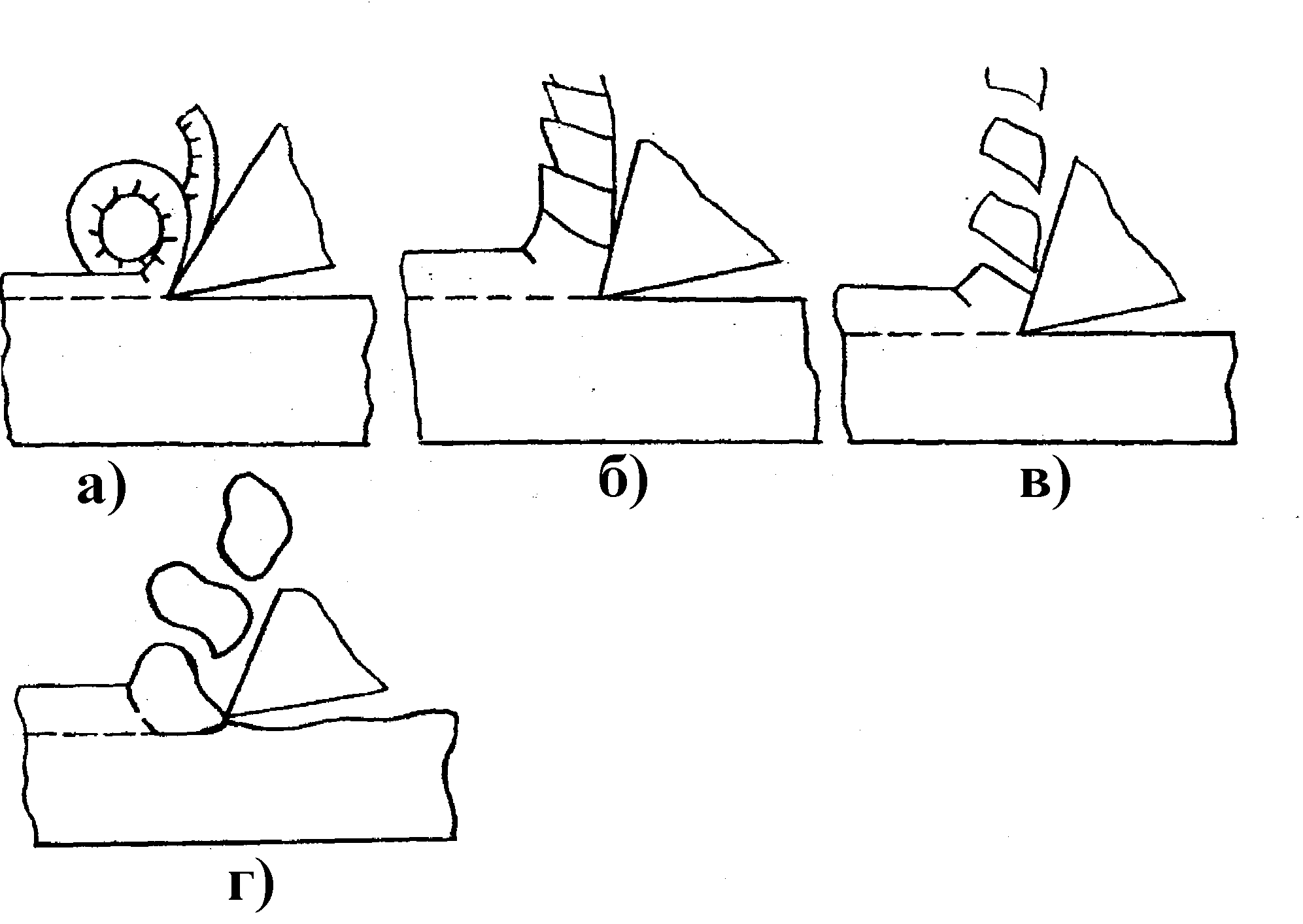
Рис.4. Типы стружек
а) сливная; б) суставчатая; в) скалывания; г) надлома
Изменяя условия резания и состояния материала, можно при его обработке получать различные типы стружек. Так, например, при резании меди с глубоким охлаждением можно получить стружки надлома, а при резании с подогревом твердых и хрупких материалов - стружки скалывания и даже сливные. При резании некоторых современных материалов, применяющихся в технике, например таких, как: высокопрочные и тугоплавкие сплавы, неметаллические, полимерные и композиционные материалы, образуются стружки, по своей форме и внешнему виду значительно отличающихся от вышеперечисленных.
В механике процесса резания металлов уделяется большое внимание стружкообразованию, так как оно определяет протекание процесса резания в целом. Hа осуществление процесса стружкообразования обычно затрачивается более 90% силы и работы резания; соответственно, при стружкообразовании выделяется основная часть тепла. От этого процесса, главным образом, зависят тепловой режим и контактные нагрузки на рабочих поверхностях инструмента, а следовательно, интенсивность и характер их износа. В непосредственной связи с процессом стружкообразования находится качество поверхностного слоя и точность обработки детали. Можно сказать, что почти все характеристики процесса резания и его практические результаты зависят от процесса стружкообразования. Протекание этого процесса в основном определяется деформированным состоянием зоны стружкообразования.
Установлено, что зона стружкообразования имеет клинообразную форму и размеры, сопоставимые с толщиной среза.
При этом пластическое деформирование срезаемого слоя начинается на линии, по которой проходят первые сдвиги обрабатываемого материала. Проходя через зону стружкообразования, обрабатываемый материал последовательно подвергается дополнительным пластическим деформациям при пересечении каждой последующей линии сдвига. Достигнув конечной границы зоны стружкообразования, обрабатываемый материал получает наибольшую степень деформации, свойственную уже образовавшейся стружке.
Концентрация пластической деформации у конечной границы зоны стружкообразования позволяет в некоторых случаях использовать упрощенное представление о том, что весь процесс деформации происходит вдоль некоторой условной плоскости сдвига ВС, наклоненной под углом φ к вектору скорости резания. Угол φ, называемый углом сдвига, является удобным параметром для характеристики направления и величины пластической деформации в зоне стружкообразования (рис.1).
Hапряженное состояние зоны резания также играет определенную роль в процессе стружкообразования. Хотя в силу особенностей этого процесса не наблюдается полного соответствия между напряженным и деформированным состоянием зоны стружкообразования, тем не менее изучение напряженного состояния позволяет более обоснованно подойти к анализу схем стружкообразования и влияния условий резания на процесс стружкообразования.
Установление напряженного состояния зоны стружкообразования является сложной задачей, которая даже для простейшего случая резания решена лишь в первом приближении. Причина этого заключается в том, что существующие аналитические и экспериментальные методы не позволяют определить напряженное состояние зоны стружкообразования без ряда допущений.
2.2.1. Методы оценки состояния зоны резания
Для качественной и количественной оценки напряженно-деформированного состояния при резании существуют различные методы.
Метод определения коэффициента усадки стружки. Внешними наблюдениями за процессом стружкообразования установлено, что в большинстве случаев обработки резанием стружка укорачивается, утолщается и становится шире срезаемого слоя ("разбухает", "усаживается"). Усадка стружки является внешним проявлением процесса деформирования при наличии больших пластических деформаций. Рассматриваются следующие геометрические соотношения (рис.5): коэффициент укорочения kl=Lo/L , коэффициент уширения kb=b1/b, коэффициент утолщения ka=a1/a. Так как объем пластически деформированного материала не изменяется, то a·b·Lo=a1·b1·L и при b1=b получим, что Lo/L=a1/a , т.е. kl=ka .
При резании различных материалов и в разных условиях эти коэффициенты могут быть больше или меньше единицы. В случае равенства линейных размеров срезаемого слоя и стружки понятие "коэффициент усадки" теряет свой смысл, так как "усадки" не происходит, а энергия, затраченная на пластическое деформирование, достаточно велика.
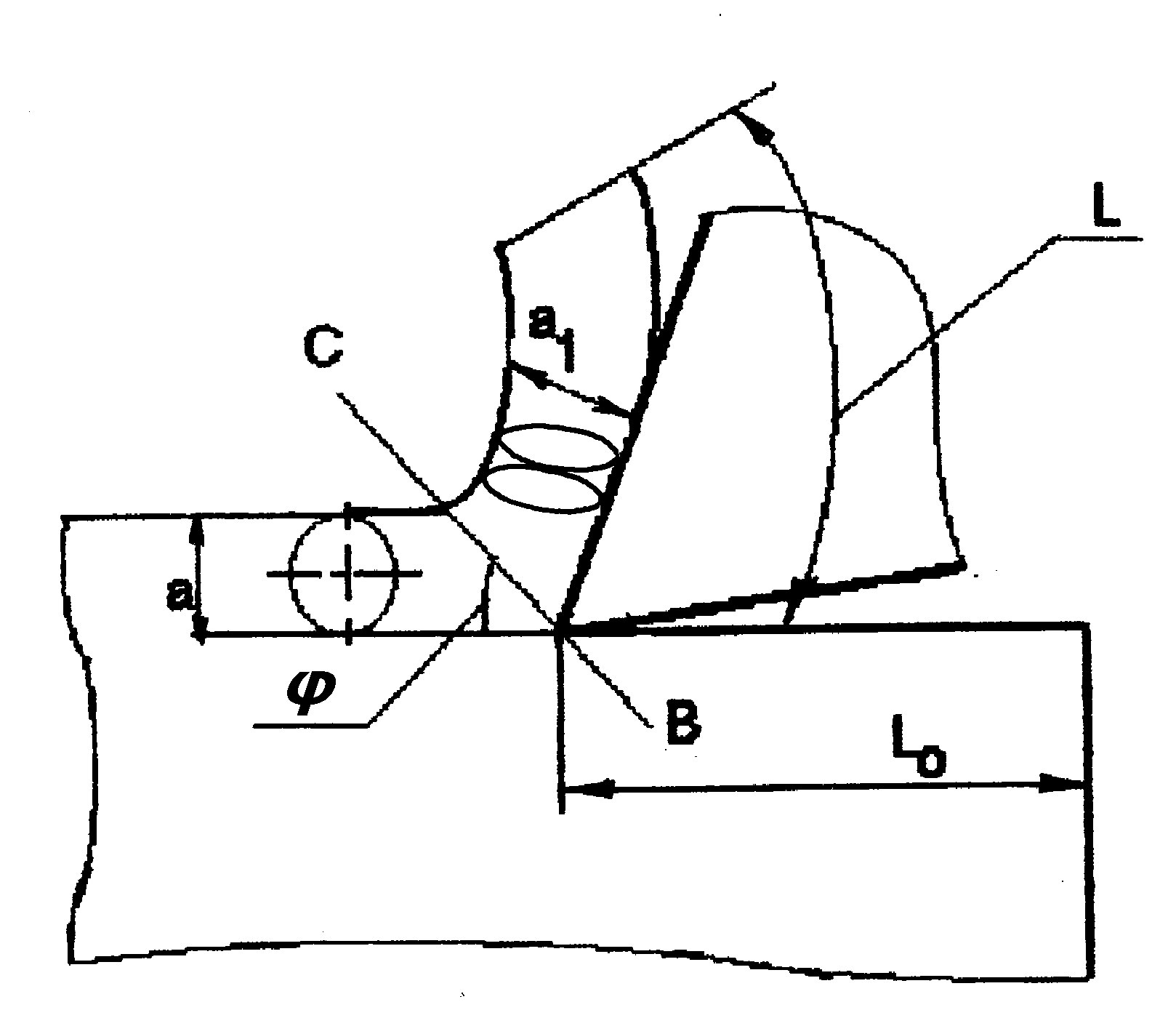
Рис.5. Схема определения величины коэффициентов усадки стружки (коэффициентов укорочения и утолщения)
Метод координатных сеток. Этот метод позволяет качественно и количественно оценить напряженно-деформированное состояние в зоне резания при образовании сливных стружек и стружек скалывания. Сетки с различной формой ячеек наносятся на наблюдаемую поверхность детали. По характеру искажения формы ячеек сеток можно получить представления о размерах зоны деформированного материала, количественных характеристиках напряженно-деформированного состояния в очаге деформации и поверхностном слое детали, а также о контактных нагрузках и трении на поверхностях режущего клина.
Метод микротвердости. Метод определения напряженного состояния по изменению микротвердости Hu деформированного материала в сочетании с методом координатных сеток позволяет, зная величины интенсивностей деформаций еi, определить величины интенсивностей напряжений бi в различных точках зоны резания. Для этого необходимо построить графики механических испытаний, связывающие еi - бi - Hu.
Поляризационно-оптические методы. Эти методы позволяют экспериментально-расчетным путем определить контактные напряжения, а также распределение касательных и нормальных напряжений в режущем клине. Инструмент необходимо изготовлять из оптически-активного материала (эпоксидная смола, стекло) и резать высокопластичные материалы (свинец, алюминий). Обработка фотографий изоклин (линий равных нормальных напряжений) и изохром (линий равных касательных напряжений) достаточно сложна и трудоемка.
Кроме перечисленных выше, достаточно часто используются методы расчета напряженно-деформированного состояния материала в зоне резания, связанные с построением поля линий скольжения, применением теории подобия и электромоделирования.
При обтекании режущего клина часть деформированного материала перемещается по передней поверхности, превращаясь в стружку, а другая часть ниже линии среза - по задней поверхности и образует поверхностный слой детали.
2.2.2. Физико-механические свойства поверхностного слоя
Формирование поверхностного слоя детали путем срезания стружки определяется сложным напряженно-деформированным состоянием зоны резания. Процесс образования поверхностного слоя деталей при резании материалов представляет собой комплекс сложных физических явлений. Физико-механические свойства поверхностного слоя оценивают глубиной hнк и степенью N наклепа, величиной и знаком остаточных напряжений, микроструктурой и другими характеристиками. Под степенью наклепа понимается отношение N=((Hmax-Ho)/Ho)·100%, где Hmax - микротвердость обработанной поверхности; Но - микротвердость исходного материала заготовки.
Изменение степени пластической деформации срезаемого слоя при увеличении скорости резания вызывает соответствующее изменение наклепа обработанной поверхности. При более высоких скоростях резания глубина наклепа снижается. При износе инструмента возрастают нормальные силы N2 и силы трения F2 на задней поверхности инструмента (рис.2) и поэтому увеличивается наклеп поверхностного слоя детали. Степень наклепа очень сильно зависит от физико-механических свойств обрабатываемого материала. Нержавеющие, жаропрочные стали и другие пластичные материалы обладают большой склонностью к наклепу.
Глубина наклепа определяется путем последовательного измерения микротвердости на косых срезах или методом рентгено-структурного анализа. Степень и глубина наклепа в основном зависят от физических свойств обрабатываемого материала, скорости резания (при больших скоростях степень и глубина наклепа уменьшаются) и угла резания (чем больше угол резания, тем больше степень и глубина наклепа). Многие пластичные материалы (стали аустенитного класса, медь, жаропрочные и титановые сплавы) обладают большой склонностью к наклепу. Увеличение подачи, износа инструмента и радиуса округления режущей кромки приводит к увеличению размеров зоны деформации, увеличению глубины и степени наклепа . Необходимо отметить, что при образовании поверхностного слоя изделия параллельно происходят два конкурирующих процесса: упрочнение ("наклеп") и разупрочнение ("отдых").
С увеличением скорости резания повышается температура и возрастает скорость разупрочнения. Высокая температура может привести к рекристаллизации и снижению наклепа, что и наблюдается при шлифовании.
Остаточные напряжения могут возникнуть в результате действия упруго-пластических деформаций, при значительном нагреве поверхностного слоя, а также при структурных и фазовых превращениях. В этих случаях атомы в поверхностном слое отклоняются от положения устойчивого равновесия, но стремятся вернуться в исходное положение - возникают внутренние силы. С увеличением нормального расстояния между атомами появляются напряжения растяжения, а при уменьшении - сжатия.
При движении инструмента по обработанной поверхности возникает пластическое растяжение поверхностных слоев в направлении линии среза. Слои, лежащие ниже, деформируются упруго и после прохода инструмента стремятся возвратиться в исходное состояние, т.е. сжаться. В поверхностном слое изделия возникают остаточные напряжения сжатия. Также под действием теплоты, идущей в деталь, верхние слои растягиваются, а нижние холодные слои оказывают сопротивление. Появляются остаточные напряжения сжатия. Иногда (при охлаждении) во внутренних слоях возникают остаточные напряжения сжатия, а на поверхности - растяжения. Результирующая эпюра остаточных напряжений зависит от интенсивности действия механического и теплового факторов. Например, интенсивный нагрев может уменьшить напряжения сжатия, возникшие от механического воздействия. При шлифовании стальных деталей поверхностный слой нагревается до высоких температур и происходят структурные преобразования. Превращения, связанные с увеличением объема структурных составляющих, могут вызвать появление остаточных напряжении сжатия, а при уменьшении объема - остаточных напряжений растяжения.
С увеличением скорости резания или уменьшением угла резания остаточные напряжения уменьшаются и могут изменить свой знак. Увеличение подачи, глубины резания и износа инструмента приводит к увеличению остаточных напряжений. Сжимающие остаточные напряжения повышают износостойкость деталей машин, усталостную прочность и их коррозионную устойчивость. Растягивающие остаточные напряжения приводят к снижению циклической прочности и появлению трещин на поверхности деталей. Остаточные напряжения бывают трех видов:
- Остаточные напряжения первого рода, уравновешивающиеся между большими объемами деформируемого тела. Они вызывают коробления и изменения формы изделия.
- Остаточные напряжения второго рода, уравновешивающиеся в объеме нескольких зерен. Они приводят к трещинообразованию.
- Остаточные напряжения третьего рода, уравновешивающиеся внутри каждого зерна, они связаны с изменением расположения атомов в кристаллической решетке.
Величину остаточных напряжений можно уменьшить путем увеличения жесткости технологической системы, правильного выбора режимов резания и геометрии инструмента, а также применением смазочно-охлаждающих жидкостей (СОЖ) и специальной термообработки изделия.
Важной характеристикой физического состояния поверхностного слоя является величина и знак остаточных напряжений. При наличии в поверхностном слое сжимающих остаточных напряжений предел выносливости деталей обычно повышается, а остаточные напряжения растяжения понижают предел выносливости. Для сталей, обладающих высокой твердостью, повышение усталостной прочности в результате сжимающих напряжений достигает 50%, а снижение ее за счет растягивающих напряжений - 30%.
Остаточные напряжение при резании металлов образуются в результате неравномерности пластической деформации и значительного нагрева поверхностных слоев. Исследования процесса формирований остаточных напряжений показали, что, если механическая обработка материала сопровождается высокими силами резания, то формируются сжимающие остаточные напряжения; при повышенных температурах в зоне резания формируются остаточные напряжения растяжения.
В производственных условиях широко используют различные способы искусственного создания в поверхностном слое обрабатываемых деталей остаточных напряжений сжатия или растяжения. Причем, эти "искусственные" напряжения должны иметь обратный знак по отношению к напряжениям, возникающим при работе детали в изделии. Например, накатываются для увеличения наклепа и, следовательно, создания сжимающих напряжений поверхности коленчатых валов, работающие в условиях растягивающих нагрузок, что повышает усталостную прочность вала на 30%-40%.
2.3. Тепловые явления. Способы измерения температуры в зоне резания
При резании почти вся механическая энергия, затрачиваемая на деформирование, разрушение и трение, переходит в тепловую. Исследования процессов теплообразования при резании позволили определить направление и интенсивность тепловых потоков, градиенты температур в контактных областях и характеристики температурного поля в зоне резания, деталью и окружающей средой, а также получить качественное и количественное представление о тепловом балансе при резании различных материалов. Знание этих закономерностей имеет большое значение для рационального конструирования и эксплуатации режущих инструментов, применения эффективных методов смазки и охлаждения, повышения точности и качества поверхности обработанных деталей.
Уравнение теплового баланса можно представить следующим образом(рис.6);
Q1+Q2+Q3=q1+q2+q3+q4 (1)
где Q1 - количество тепла, эквивалентное энергии, затраченной на деформирование и разрушение при стружкообразовании и формировании поверхностного слоя;
Q2 - количество тепла, эквивалентное работе сил трения при контакте передней поверхности клина и деформированного материала;
Q3 - количество тепла, эквивалентное работе сил трения на задней поверхности клина при переходе деформированного материала в поверхностный слой детали;
q1 - количество тепла, уходящее в стружку;
q2 - количество тепла, идущее в деталь;
q3 - количество тепла, переходящего в режущий инструмент;
q4 - количество тепла, передающееся окружающей среде.
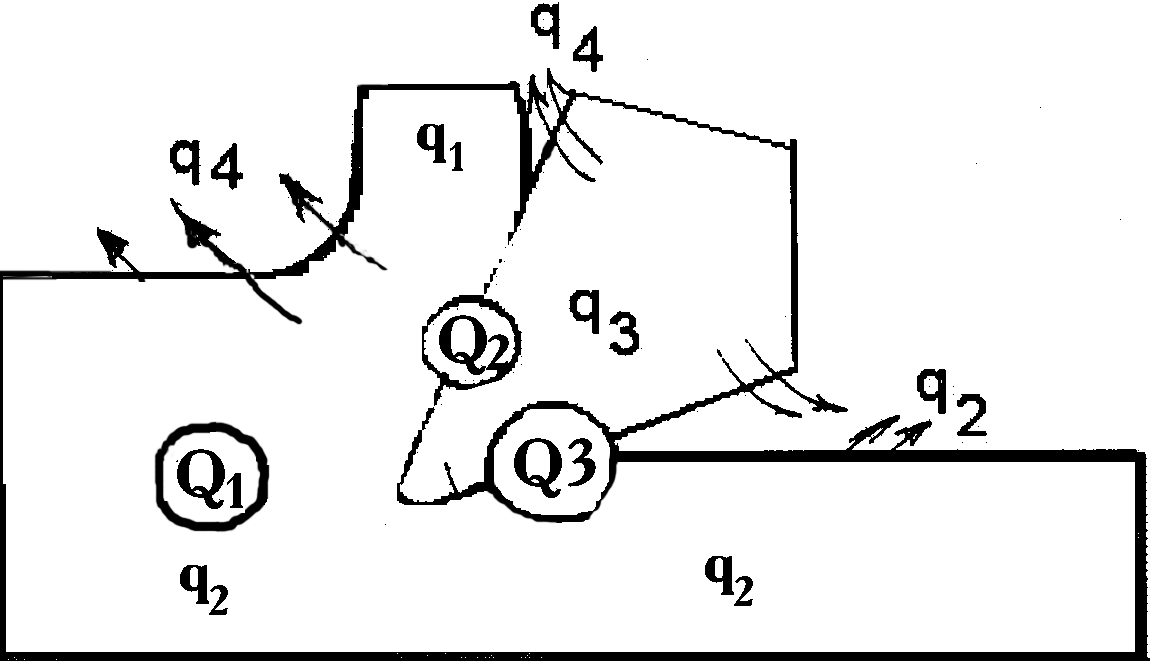
Рис.6. Схема распространения тепловых потоков
Количественное выражение уравнения теплового баланса зависит от физико-химических свойств материалов заготовки и инструмента, геометрических параметров режущего инструмента, режимов резания и условий обработки. Например, при резании различных конструкционных материалов и сплавов наибольшее количество тепла уходит со стружкой, а в процессе шлифования - в деталь. При резании жаропрочных и титановых сплавов, имеющих плохую теплопроводность и низкие коэффициенты температуропроводности, значительное количество тепла концентрируется в контактной зоне или переходит в режущий инструмент.
Исследования тепловых явлений при механической обработке металлов сложно из-за высоких контактных (инструмент-стружка) давлений и температур в зоне резания. Поэтому используемые электрические и математические методы определения температур дают только относительные представления о температурных явлениях при резании.
Наиболее распространенными являются методы, позволяющие измерять температуру отдельных участков зоны резания и режущего инструмента. К ним относятся: методы термопар (рис.7) и рентгено-структурного анализа, радиационно-оптический метод. Измерение температур в узких областях зоны резания с помощью термопар впервые предложено Я.Г.Усачевым в 1912 году. В случае применения "искусственной термопары" в режущей части инструмента просверливается отверстие, в которое вставляется термопара с изолированными проводниками диаметром 0,3-0,5 мм. Место спайки термопары располагают, как можно ближе к нагретым поверхностям инструмента. Температуру оценивают по изменению величины термоэлектродвижущей силы.
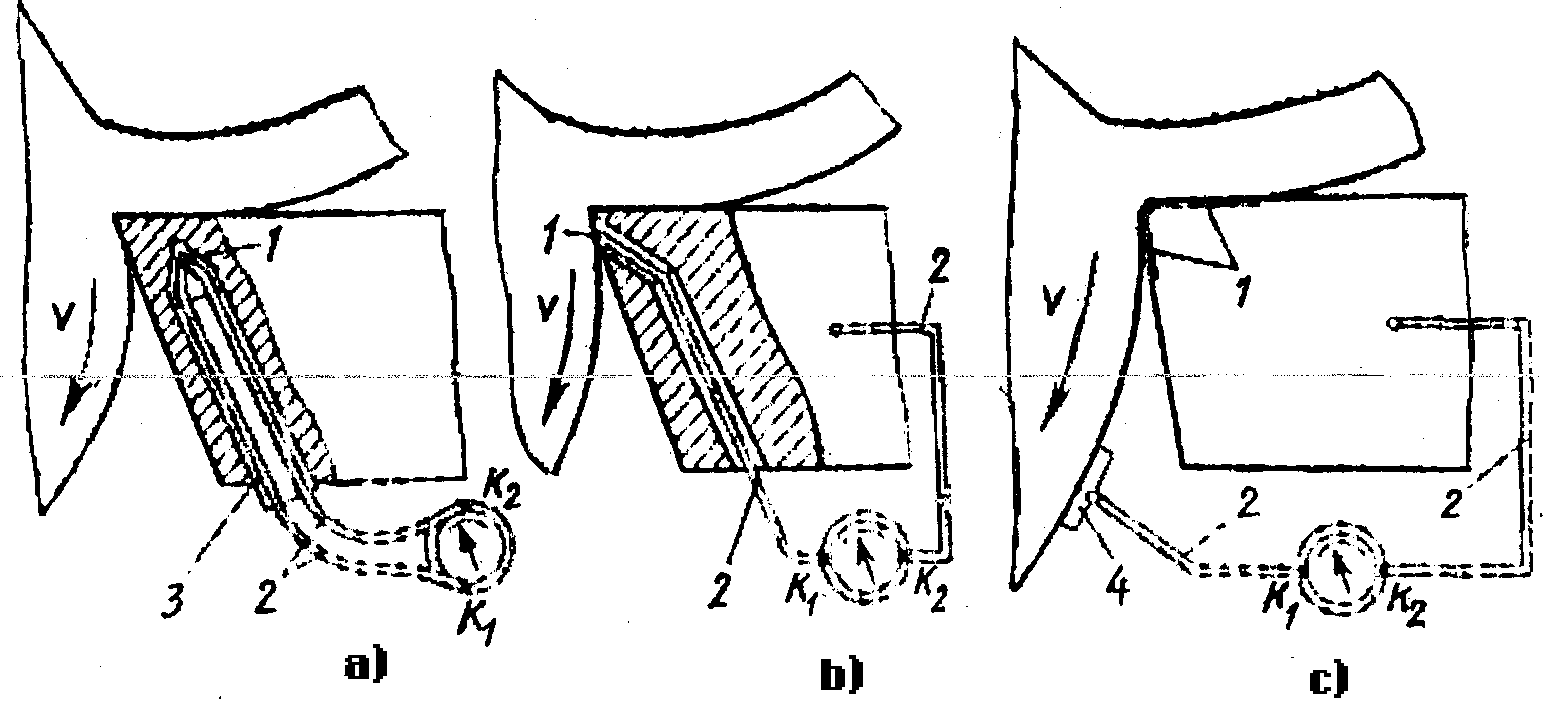
Рис.7. Схемы термопар:
а - искусственная; b - полуискусственная; c - естественная.
В другом варианте термопары, получившем название "полуискусственная", один изолированный проводник выводится на заднюю или переднюю поверхности инструмента и расклепывается. Вторым проводником является тело инструмента, что значительно упрощает схему измерения. Идеи Я.Г.Усачева нашли дальнейшее применение и развитие в исследованиях отечественных и зарубежных ученых (созданы конструкции привариваемых, прижимных, защемленных, подвижных, бегущих и других видов термопар). Значительное распространение получила так называемая "естественная термопара". Здесь проводниками являются инструмент и деталь, а спаем термопары - область контакта задней и передней поверхности режущего клина с металлом заготовки.
Вопросы теоретического расчета температурного поля при резании представляют значительный научный интерес. Под термином "температурное поле" в зоне резания подразумевается совокупность различных значений температур во всех точках деформированного объема материала в данный момент времени.
Первые попытки расчета поля температур сводились к использованию решений классических задач теории теплообмена в твердых телах. Температура резания определялась решением общего уравнения теплопроводности:
(2)
где: a =l /(c r) - коэффициент температуропроводности;
λ - коэффициент теплопроводности;
c - теплоемкость;
ρ - удельный вес материала;
Для решения этого уравнения необходимо задаться определенными граничными условиями, связанными с характеристиками реального процесса резания. Математическое описание условий теплообмена на граничных поверхностях зоны деформации представляет значительные трудности. Поэтому многие исследователи вводили целый ряд допущений и упрощений, значительно снижая ценность решения задачи. Конечные формулы отличались громоздкостью, содержали большое количество трудноопределяемых коэффициентов и были неудобны для практического использования.
Наиболее плодотворным методом интегрирования уравнения теплопроводности является метод источников тепла. Линеаризация уравнения (2) производится путем осреднения теплофизических коэффициентов в узком интервале температур, выражение мощности источников через линейную функцию температуры и принятия постоянной скорости перемещения источника. При этом не учитываются тепловые эффекты фазовых и структурных превращений. Метод источников тепла дает возможность путем несложных преобразований представить температуру поля в виде определенного интеграла или сходящегося ряда и таким образом количественно описать процессы распространения тепла при резании линейных, плоских и пространственных задач. Источники тепла рассматриваются как местные, сосредоточенные или распределенные, неподвижные и подвижные, мгновенные н длительного действия.
Распространение тепла от подвижного сосредоточенного источника рассматривается, как совокупность наложенных друг на друга процессов выравнивания теплоты мгновенных элементарных источников. При этом координаты точек температурного поля x , у , z перемещаются вместе с подвижным источником ( рис. 8).
Тепло Q, внесенное в точечный элемент (R = 0) неограниченного теплопроводного тела в момент времени t = 0, выравнивается по экспоненциальному закону
(3)
где R2 = x2 + y2 + z2 - радиус-вектор, т.е. расстояние элемента поля (точка А) от источника (точка В). Уравнение (3) является главным решением метода источников.
На рис.9 приведены температурные поля, полученные разными исследователями экспериментальным путем (радиационно-оптическим методом) и рассчитанные по методу источников при свободном резании (точении) стали в одинаковых условиях. Характер распределения температур в зоне резания хорошо согласуется с современными представлениями о поле деформаций, а наибольшие температуры возникают в области максимальных деформаций и на контактных площадках.
2.4. Физические явления в зоне контакта инструмента и обрабатываемого материала
Физические и химические процессы на поверхностях контактирующих тел весьма многообразны и сложны. На передней поверхности инструмента образуются налипы и наросты, изменяющие характер стружкообразования, ухудшающие качество обработанной поверхности и разрушающие режущую кромку. В контактной области возникает целый ряд поверхностных явлений: адгезия, коррозия, диспергирование, упрочнение и разупрочнение поверхностных слоев, диффузия, адгезия, эрозия, окисление и другие физико-химические явления. Даже такое беглое перечисление подчеркивает высокую сложность процессов трения при срезании металла режущим инструментом.
Трение при обработке резанием имеет свои специфические особенности, которые в основном сводятся к следующим:
возникают различные виды трения (граничное и жидкостное встречаются редко);
особую роль играет чистое трение, приводящее к интенсивному разрушению режущего клина;
взаимное соприкосновение трущихся поверхностей заготовки и режущего инструмента происходит только один раз и носит сложный характер; причем физический микро- и субмикрорельеф не имеют ничего общего с технологическим микрорельефом обработанной поверхности, образующимся при различных видах обработки (точении, сверлении, фрезеровании и др.);
трение происходит при очень больших давлениях, высоких температурах, доходящих до температур плавления, и значительных истинных площадях контакта;
сложное распределение нормальных и касательных нагрузок по контактным поверхностям инструмента (рис.10).
большие переменные значения коэффициента трения ( m ³ 1), объясняющиеся интенсивной адгезией и диффузией. Величина среднего коэффициента трения в основном зависит от скорости резания (скорости нагружения), толщины среза и величины переднего угла режущего клина;
сложное взаимное влияние вибраций и вида трения;
жесткий режим трения, приводящий к появлению наростов и интенсивному разрушению поверхностных слоев режущего клина.
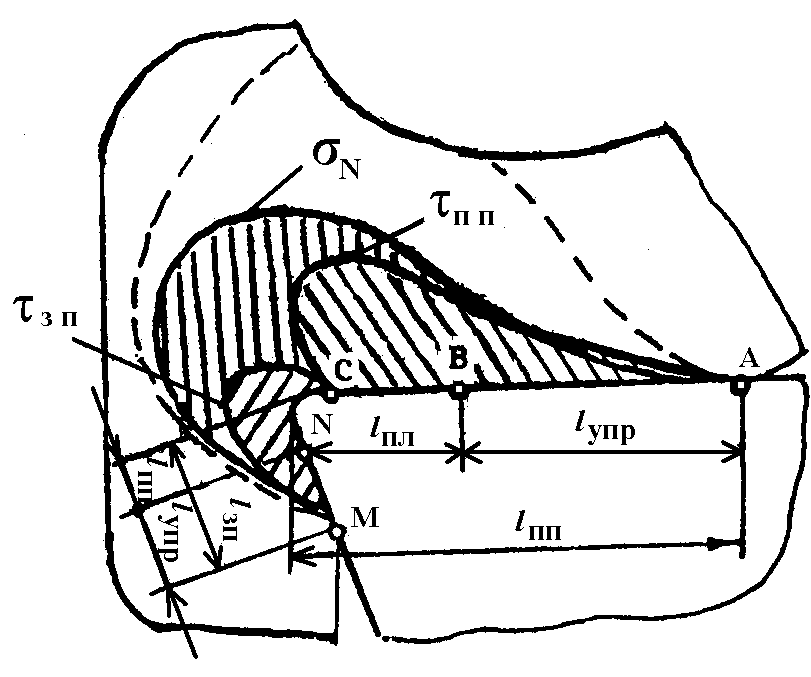
Рис.10. Схема распределения контактных нагрузок на передней и задней поверхностях инструмента
t пп – касательные нагрузки на передней поверхности;
t зп – касательные нагрузки на задней поверхности;
lпл – длина пластического контакта;
lупр – длина упругого контакта;
C - точка, в которой t = 0.
2.4.1. Наростообразование
При некоторых условиях резания на передней поверхности инструмента появляется слоистое металлическое образование, называемое наростом. Существует много различных гипотез о причинах возникновения наростов, что свидетельствует о малой изученности природы наростообразования. Наростообразование находится в тесной взаимосвязи с условиями трения, высокими контактными температурами и давлениями. Наиболее вероятной причиной наростообразования можно считать возникновение несимметричной клинообразной застойной зоны упрочненного материала впереди режущего клина, а также торможение (схватывание) тонких контактных слоев стружки на шероховатой передней поверхности инструмента (рис.11) вследствие наличия чистого трения, высоких коэффициентов трения и значительной реальной площади контакта.
Нарост обладает особыми свойствами:
а) имеет неоднородную слоистую структуру, существенно отличающуюся от структуры обрабатываемого материала и материала режущего инструмента;
б) нарост обладает высокой твердостью и значительной вязкостью. Однако большие силы трения (резания) и высокая температура в зоне контакта приводит периодичности образования нароста.

Рис.11. Схема наростообразования и влияние нароста на размер детали: Lн - длина нароста; hн - высота нароста; bн и dн - соответственно углы заострения и резания при наличии нароста; b и d - соответственно углы заострения и резания инструмента; D и Dн-соответствующие диаметры детали
Частота срывов нароста увеличивается (до нескольких сотен раз в минуту) с возрастанием скорости резания, уменьшением переднего угла и увеличением толщины срезаемого слоя.
Hаростообразование зависит от физико-механических свойств обрабатываемых материалов и материалов режущих инструментов. Hарост может появляться при резании твердосплавным, быстрорежущим, минерало-керамическим и алмазным инструментами различных материалов (в том числе и при обработке чугуна, титановых, жаропрочных и других сплавов). Hаибольшей величины наросты достигают при резании пластичных металлов с образованием сливной стружки и инструментами, изготовленными из углеродистых и быстрорежущих сталей.
Hарост образуется в основном тогда, когда температура инструмента больше температуры стружки и контактные слои стружки тверже ее внутренних слоев. При этом сила трения на контактной поверхности больше сил сцепления частиц в стружке, а скорость их перемещения по мере удаления от поверхности контакта возрастает и доходит до величины скорости стружки.
Pазмеры нароста с увеличением скорости резания вначале увеличиваются, а затем уменьшаются. Причем сначала уменьшается длина, а при более высоких скоростях - высота нароста. При увеличении переднего угла размеры нароста (в основном высота) уменьшаются.
Hарост обладает высокой твердостью и значительной вязкостью. Твердость нароста в 2-3 раза выше твердости исходного материала и резко снижается с повышением температуры резания. Объясняется это тем, что с увеличением температуры резания происходит рекристаллизация материала нароста, контактные слои стружки теряют свою твердость, градиент твердости слоев нароста выравнивается, твердость нароста монотонно уменьшается. Вследствие этого прекращается увеличение размеров нароста и он срывается.
Периодические срывы нароста находятся в тесной связи с рекристаллизацией и фазовыми превращениями, при которых и происходит понижение твердости и прочности (разупрочнение) материала наростов. Hарост теряет свою режущую способность, раздавливается и уносится стружкой или вдавливается в обработанную поверхность. Частота срывов нароста увеличивается с возрастанием скорости резания, подачи и уменьшением переднего угла.
Hаличие на передней поверхности инструмента упрочняющей фаски с передним углом, равным нулю или отрицательным, делает нарост более устойчивым.
Изменение величины коэффициента усадки стружки и силы резания с увеличением скорости резания носит сложный характер. При небольших скоростях резания происходит интенсивное наростообразование, нарост уменьшает угол резания и тем самым сопротивление резанию. При увеличении скорости нарост срывается и угол резания принимает исходное значение. Сопротивление резанию увеличивается. При скоростях V = 60-100 м/мин. нарост не образуется.
Явление наростообразования имеет большое значение в практике обработки резанием(рис.12):
1) нарост изменяет величину угла резания , а следовательно,изменяет сопротивление резанию и условия трения;
2) нарост ухудшает шероховатость обработанной поверхности;
3) нарост защищает заднюю поверхность инструмента от разрушения и изменяет размеры детали;
4)периодические срывы нароста приводят к возникновению вибраций, ухудшающих качество обработки;
5) нарост не допустим при чистовой обработке;
6) наросты могут образовываться при резании твердосплавными, быстрорежущими, минералокерамическими и алмазными инструментами различных материалов. Но наибольшей величины наросты достигают при резании пластичных металлов.
Управление процессом наростообразования обеспечивается правильным выбором режимов резания,геометрией инструмента, применением смазочно-охлаждающих веществ и т.п.
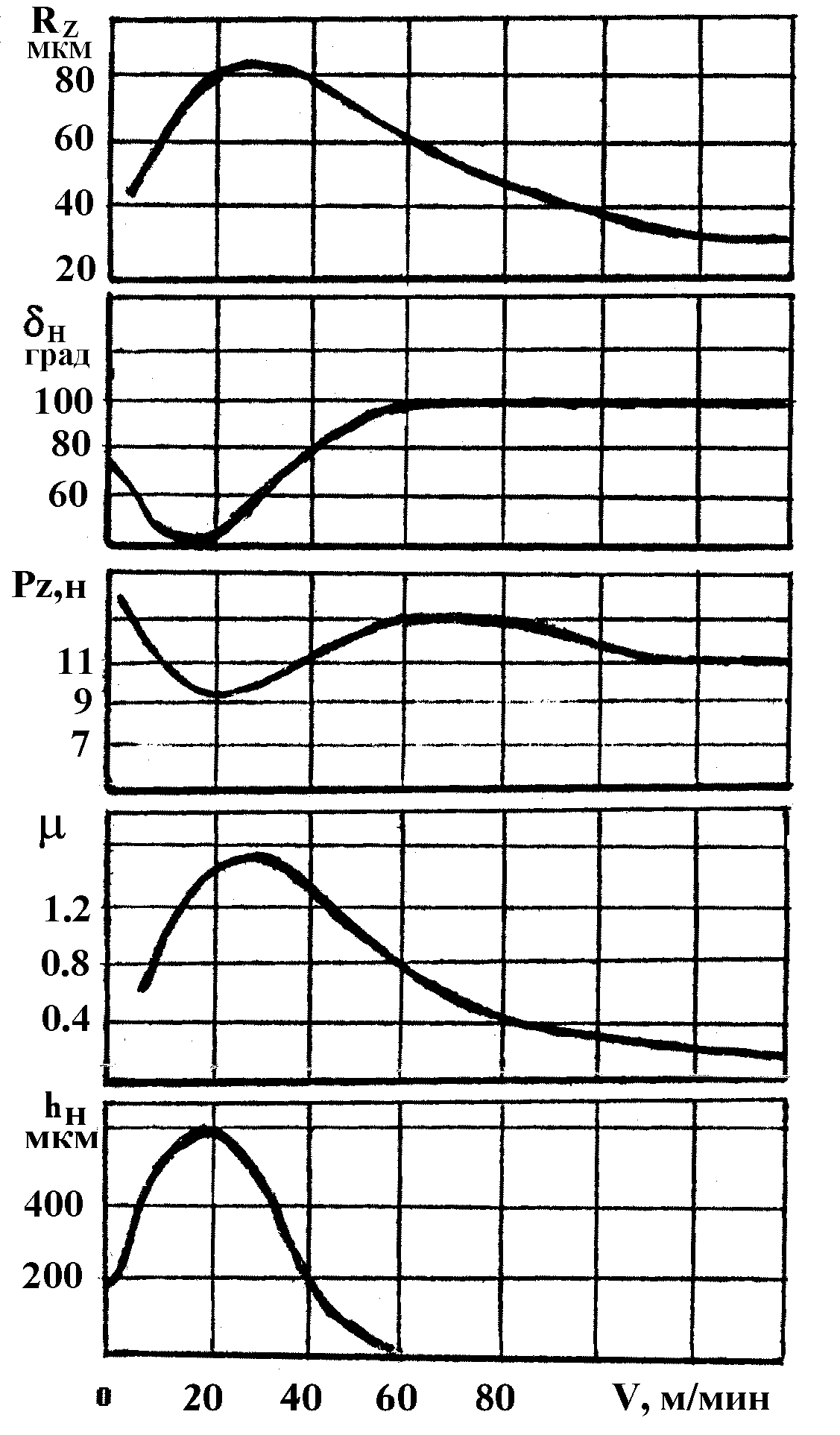
Рис.12. Влияние высоты нароста на величину шероховатости Rz, угол резания dн, силу резания Рz и коэффициент трения m при резании стали 40Х на различных скоростях резания V